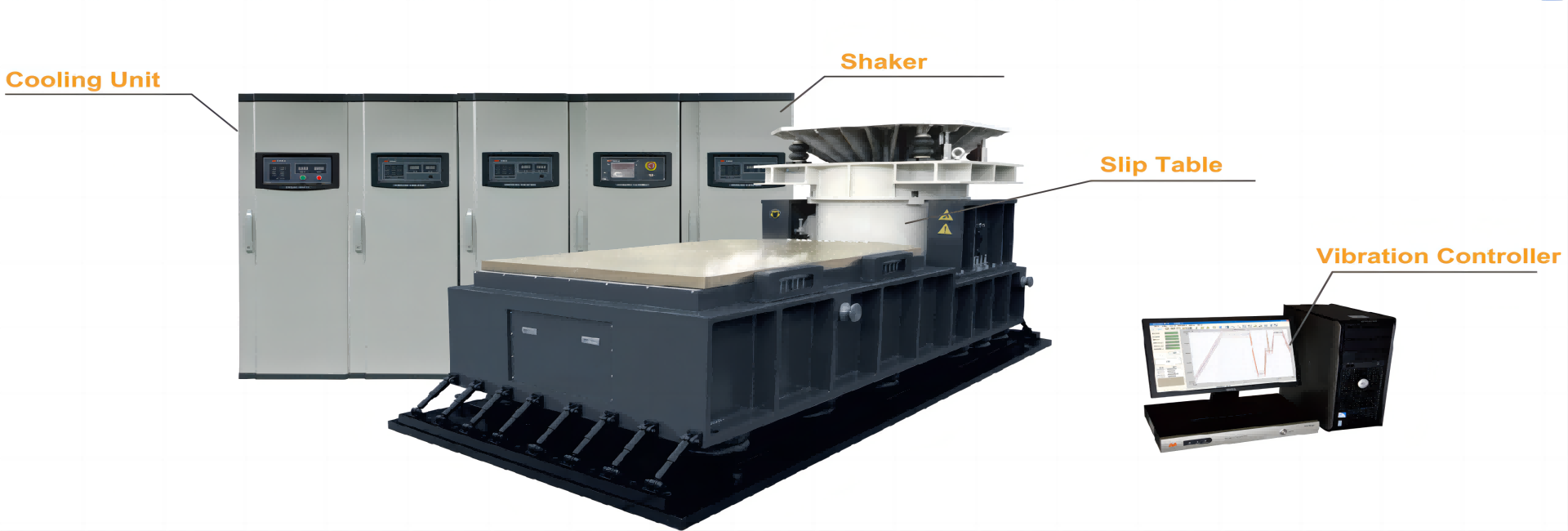
PRODUCT CATALOG
- Air-cooled Electric Vibration Shaker Testing Machine
- Water-cooled Electric Vibration Sharker Testing System
- Inductive Electric Vibration Table Testing System
- Vertical Extension Table for Vibration Testing Equipment
- Horizontal Slide for Vibration Testing Equipment
- Triaxial Vibration Test System
- Six-degree of Freedom Electrodynamic Vibration Testing System
- Electric Ejection Arrester Test Bench for Shock Vibration Testing
- Smart Power Amplifier for Vibration Test Table
- Pneumatic Vertical Shock/Crash Vibration Test Bench System
- Hydraulic Vertical Impact Vibration Test Bench Equipment
- Pneumatic Two-way Vertical Impact Test Bench for Shaker Testing
- Steady-state Acceleration Vibration Testing Bench Machine
- Hydraulic Vibration Test Bench for Hydraulic Vibration Shaker Testing
- Hydraulic Tilt and Swing Vibration Test Bench Equipment
Your Location : Home >> Product Center / Horizontal Slide for Vibration Testing Equipment / FUJI VIBRATION HBT SLIP TABLES HYDROSTATIC-BEARING SLIP
Name | FUJI VIBRATION HBT SLIP TABLES HYDROSTATIC-BEARING SLIP |
Rated thrust (sine): | 1kN |
Rated thrust (random): | 1kN |
Rated thrust (impact): | 2kN |
Rated sinusoidal acceleration: | 980m/s2 |
Rated random acceleration: | 784m/s2 |
Vertical platform weight: | 65kg |
First-order resonance frequency response: | 8500Hz(±5) |
Shaker body size (LWH): | 330mm300mm330mm |
Frequency range: | 5-10000Hz |
Rated displacement p-p: | 20mm |
Rated speed: | 2m/s |
Quality of moving parts: | 0.8kg |
Diameter of moving coil: | Ф85mm |
Product Description
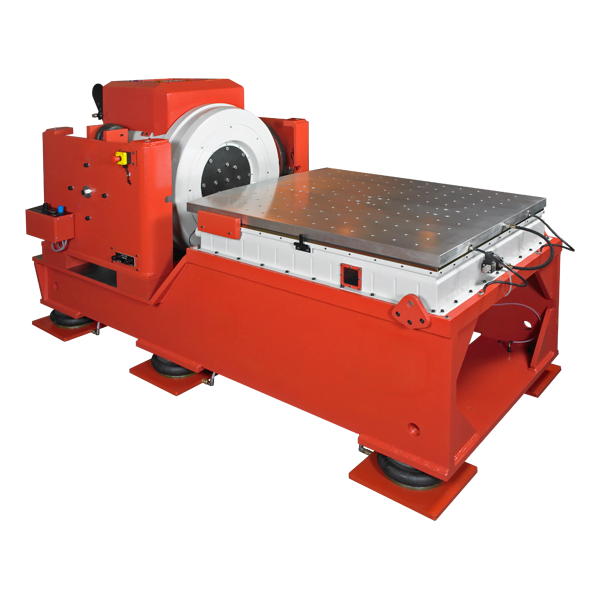
FUJI VIBRATION HBT SLIP TABLES HYDROSTATIC-BEARING SLIP
Extend your testing capabilities with our head expanders and thermal barriers, designed for our electrodynamic shakers and FUJI systems, providing force ratings of at least 9.8 kN
USE SCENARIOS
l Increasing the effective mounting surface of a shaker’s armature
l Accommodating larger, bulkier payloads
l Increasing the quantity of articles that can be tested at one time, reducing total testing times
l Providing increased flexibility in fixture design
While it is possible to purchase a stand-alone slip table for retrofitting with an existing shaker, the combo option is preferable in most cases, as the former is a more expensive, time-consuming endeavour that involves system downtime for installation and regular calibration, potential misalignment issues, and ongoing maintenance costs.