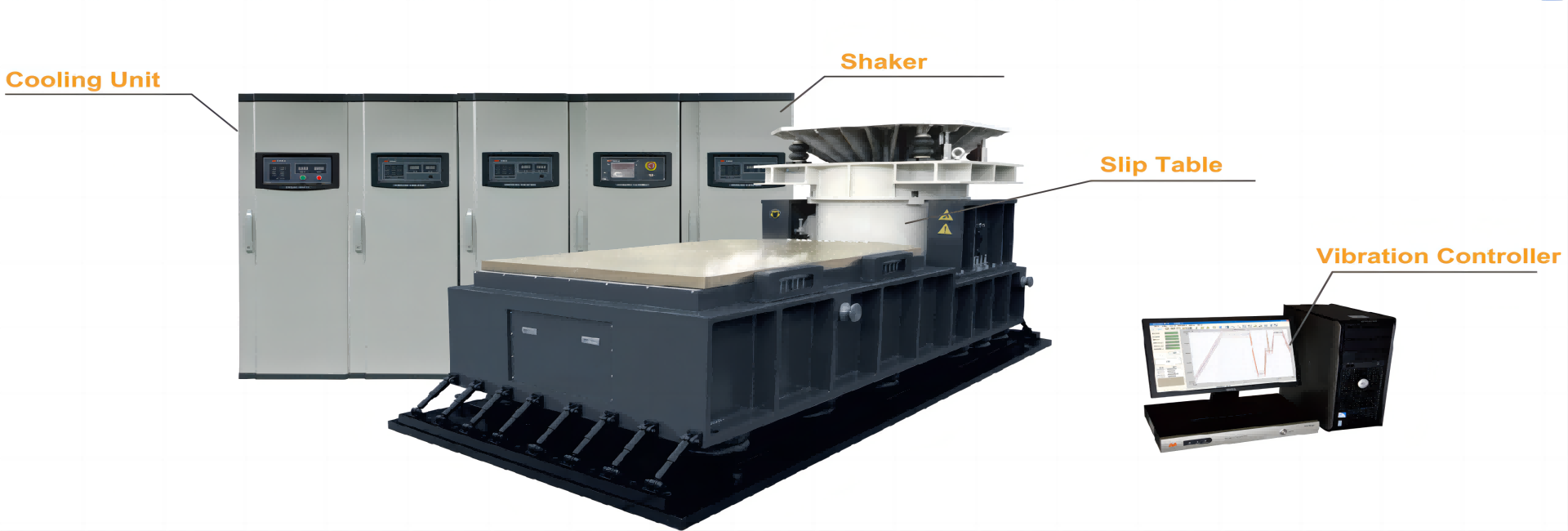
PRODUCT CATALOG
- Air-cooled Electric Vibration Shaker Testing Machine
- Water-cooled Electric Vibration Sharker Testing System
- Inductive Electric Vibration Table Testing System
- Vertical Extension Table for Vibration Testing Equipment
- Horizontal Slide for Vibration Testing Equipment
- Triaxial Vibration Test System
- Six-degree of Freedom Electrodynamic Vibration Testing System
- Electric Ejection Arrester Test Bench for Shock Vibration Testing
- Smart Power Amplifier for Vibration Test Table
- Pneumatic Vertical Shock/Crash Vibration Test Bench System
- Hydraulic Vertical Impact Vibration Test Bench Equipment
- Pneumatic Two-way Vertical Impact Test Bench for Shaker Testing
- Steady-state Acceleration Vibration Testing Bench Machine
- Hydraulic Vibration Test Bench for Hydraulic Vibration Shaker Testing
- Hydraulic Tilt and Swing Vibration Test Bench Equipment
Your Location : Home >> Product Center / Inductive Electric Vibration Table Testing System / FJ-EV203-220 Electrodynamic Shaker Vibration Test System
Name | FJ-EV203-220 Electrodynamic Shaker Vibration Test System |
Place of Origin: | China |
Brand Name: | FUJIVIBRATION |
Certification: | ISO,CE |
Model Number: | FJ-EV203-220 |
Minimum Order Quantity: | 1 set |
Price: | Negotiable |
Payment Terms: | T/T |
Packaging Details: | International standard plywood case |
Product Description
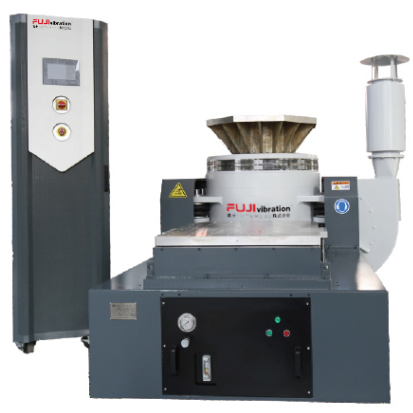
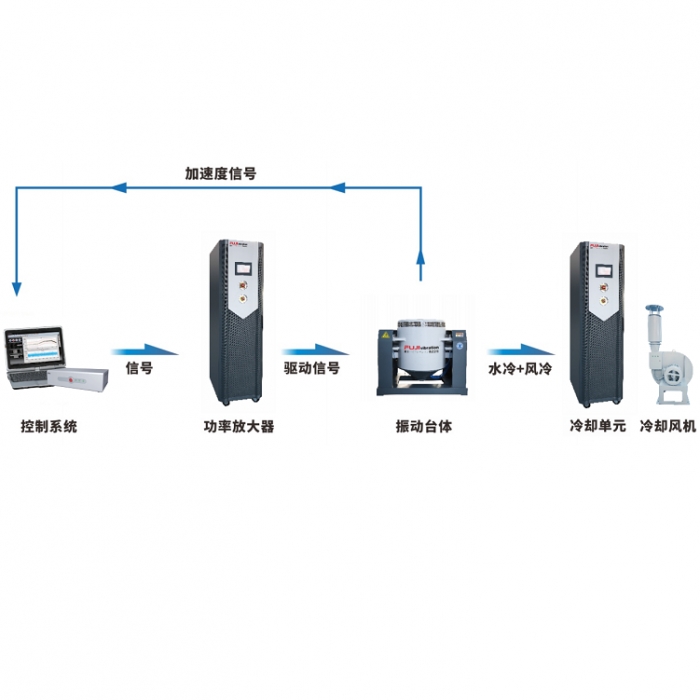
FJ-EV series of electrodynamic shaker vibration test System simulate the vibration environment under the laboratory condition, and test the impact strength as well as reliability of various vibration test applications.
FJ-EV series of electromagnetic vibration testing system simulate the vibration environment under the laboratory condition, and test the impact strength as well as reliability of various vibration test applications. In the laboratory, with the aid of vibration testing system, simulations of reproduction of sinusoidal, random, resonant search and dwell, classical shock and road models, etc. can be achieved. It is essential for product quality assurance, new product research and development.
Main Features
Rugged suspension system and linear motion guiding, strong carrying capacity, good guiding functions, high stability
Load center airbag has high static stiffness and low dynamic stiffness, strong carrying capacity, perfect performance on amplitude variation
High efficiency D class power switching, 3-sigma peak current, provide finest power consumption and minimize harmonic distortion
Quick self-diagnosis with safety interlock, high safety reliability
Airbag shock isolation device for vibration platform without the need of additional foundation, perfect reproduction of vibrational wave and reduce vibration transmittance
Provide horizontal and vertical expansion platform for different application
Simple controller operation
Technical Specifications: FJ-EV203~FJ-EV220
Model | FJ-EV203 | FJ-EV206 | FJ-EV210 | FJ-EV220 |
Shaker Model | VG300/40 | VG300/50 | VG1000/50 | VG2000/50 |
Frequency(Hz) | 2-2500 | 2-3000 | 2-3000 | 2-2500 |
Max Exiting Force(kg.f) | 300 | 600 | 1000 | 2000 |
Max. Displacement (mm p-p) | 40 | 51 | 51 | 51 |
Max. Acceleration(g) | 100 | 100 | 100 | 100 |
Max. Velocity(cm/s) | 120 | 200 | 200 | 200 |
Payload(kg) | 200 | 200 | 200 | 300 |
Armature Mass(kg) | 3 | 6 | 10 | 20 |
Armature Diameter(mm) | φ150 | φ200 | φ240 | φ320 |
Cooling Method | Forced Air Cooling | |||
Vibration Generator Weight(kg) | 460 | 920 | 1100 | 1600 |
Shaker Dimension L*W*H(mm) | 750*555*670 | 800*600*710 | 845*685*840 | 1200*870*1100 |
Power Amplifier | Amp3k | Amp6k | Amp12k | Amp22k |
Cooling Method | Forced Air Cooling | |||
Power Amplifier Weight(kg) | 250 | 320 | 350 | 500 |
Power Amplifier Dimension L*W*H(MM) | 800*550*1250 | 800*550*1250 | 800*550*1520 | 800*550*1520 |
Utility Requirements | 3-phase AC380V ±10% 50Hz | |||
Aggregate Capacity(KW) | 9 | 20 | 25 | 35 |
Applications of Dynamic Shakers:
Automotive parts and systems – qualification testing
Electronic assembly, computer equipment testing
Avionics and military hardware testing
Satellite component testing
Product and package testing
General stress screening
Performance of Dynamic Shaker
The maximum acceleration level of an electromagnetic shaker is determined by the maximum current and the loading condition. At low frequency, displacement of moving part is limited such that the acceleration will not reach high level. The resonance frequency of the moving element is designed to be higher than the upper limit of the frequency range of the shaker.
Selection of Shaker Model
To choose a suitable vibration test system, the most important thing is to know the exciting force required to perform the vibration test. To evaluate and calculate the exciting force, the following data should be specified:
Frequency (frequency range)
Maximum Acceleration
Maximum Displacement
Maximum Velocity
Specimen Mass and Fixation
The specimen fixation is selected based on the upper limit of test frequency and specimen size, either vertical expansion platform or horizontal slip table. Specimen mass is needed to evaluate the required exciting force for vibration test.